Airbag Lifts Provide Clean Power
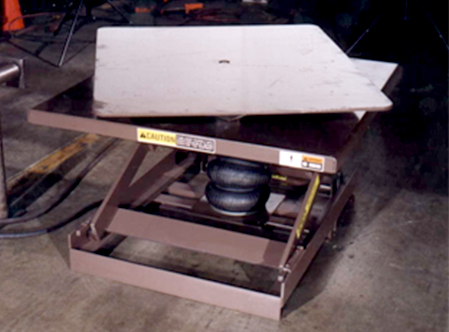
Introduction
Airbag-actuated workstation lift and turntable combination provides a clean method at a food processing plant.
Project Challenge
A major food processor needed to improve their pallet build-up and break-down process by adding a material lift that would meet the following criteria:
1) improve work station ergonomics
2) increase throughput
3) be fluid-free (so as to not contaminate the product being handled)
4) needs to be portable – to be used at more than one work station
Our Solution
Pallet build-up and/or breakdown workstations are benefited most from a solution that provides the operator incremental adjustments in both elevation and in rotation. A standard pneumatic airbag lift was recommended because the application required contamination-free actuation/operation, and because precise positioning was not necessary. The lift needed only to provide approximate adjustments in elevation in order to always keep the top layer of product being loaded/unloaded at an optimum, ergonomic work height.
The ability to rotate the pallet is also critical in order to minimize walking around the pallet during build-up/break-down. Autoquip also designed the lift base with fork “pockets” in order for the unit to be easily relocated and positioned between workstations by a fork truck, walkie, or pallet jack. The customer now has a cost-effective solution to their palletizing challenges. Relocation is simple and no electricity is required, just standard shop air supply.
Lift Specifications for this Unique Application:
Turntable Model: SR4-48-40
Lift/Turn Capacity: 4,000 lbs.
Vertical Travel: 24″
Degrees of Rotation: 360
Turntable Platform: 48″ x 48″
Actuation: Pneumatic (Lift)
The Results
Through the use of this clean, cost-efficient pneumatic lift with manual turntable, the pallet build-up/break-down task has been made more ergonomic and productive, and can be readily moved between several workstations.